Pdf to cad – PDF to CAD: It sounds simple, right? Just throw your PDF into a program and
-poof* – perfect CAD drawings. Not quite. Converting PDFs to CAD files can be a real headache, depending on the PDF’s origin and complexity. We’ll explore different methods, from super-fast automated tools to painstaking manual tracing, weighing the pros and cons of each approach.
Think of it as a deep dive into the world of digital drafting, where accuracy and efficiency are king (or queen!).
This guide breaks down the entire PDF to CAD conversion process, covering everything from choosing the right software and pre-processing techniques to understanding the limitations and maximizing accuracy. We’ll also look at the costs involved and how to get the best bang for your buck. Whether you’re an architect wrestling with scanned blueprints or an engineer dealing with complex technical drawings, this guide will equip you with the knowledge to conquer your PDF-to-CAD challenges.
PDF to CAD Conversion Methods
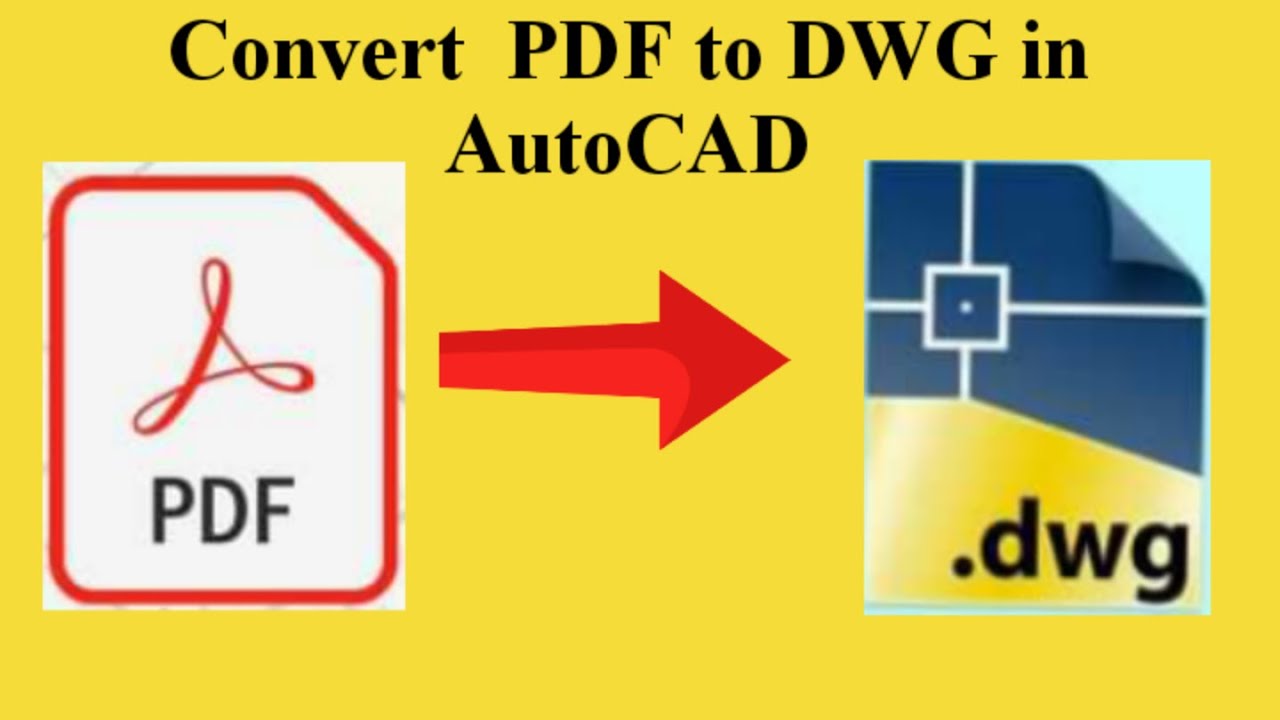
Converting PDFs to CAD formats can be a real headache, especially if you’re dealing with complex drawings. There are several approaches, each with its own strengths and weaknesses, impacting accuracy, speed, and cost. Choosing the right method depends heavily on the PDF’s complexity, your budget, and the level of accuracy you need.
Vectorization
Vectorization is a process that converts raster images (like those in PDFs) into vector graphics. This means converting the pixel-based image into a series of lines, curves, and shapes that can be easily manipulated in CAD software. Software uses algorithms to identify lines and curves in the PDF, creating vector representations. The accuracy of this method depends heavily on the quality of the original PDF.
Clean, sharp lines are much easier to vectorize than blurry or pixelated ones. While it can be quite fast for simple PDFs, complex drawings might require significant manual intervention to correct errors. The cost is relatively low if using free or inexpensive software, but professional vectorization services can be expensive.
Manual Tracing
This method involves manually redrawing the PDF content in a CAD program. It’s incredibly time-consuming, but it offers the highest level of accuracy. You have complete control over the final result, allowing for corrections and refinements not possible with automated methods. However, manual tracing is expensive due to the labor involved. It’s best suited for high-value projects where precision is paramount, such as architectural blueprints or detailed mechanical drawings.
Software used here is less important than the skill of the person tracing.
Automated Conversion Software
Several software applications specialize in converting PDFs to CAD formats. These programs employ various algorithms to automatically analyze the PDF and create a CAD representation. The speed and accuracy vary significantly between different software packages. Some programs excel at converting simple line drawings, while others struggle with complex designs containing text, shading, or images. Cost ranges from free (with limitations) to quite expensive for professional-grade software.
The ease of use varies greatly; some are very user-friendly, while others have steep learning curves.
Comparison of Conversion Methods
Method | Accuracy | Speed | Cost |
---|---|---|---|
Vectorization (Software-Based) | Moderate to High (depending on software and PDF quality) | Moderate to High (depending on complexity) | Low to Moderate |
Manual Tracing | Very High | Very Low | High |
Automated Conversion Software | Low to High (depending on software and PDF quality) | High to Moderate (depending on complexity) | Low to High |
Software and Tools for Conversion
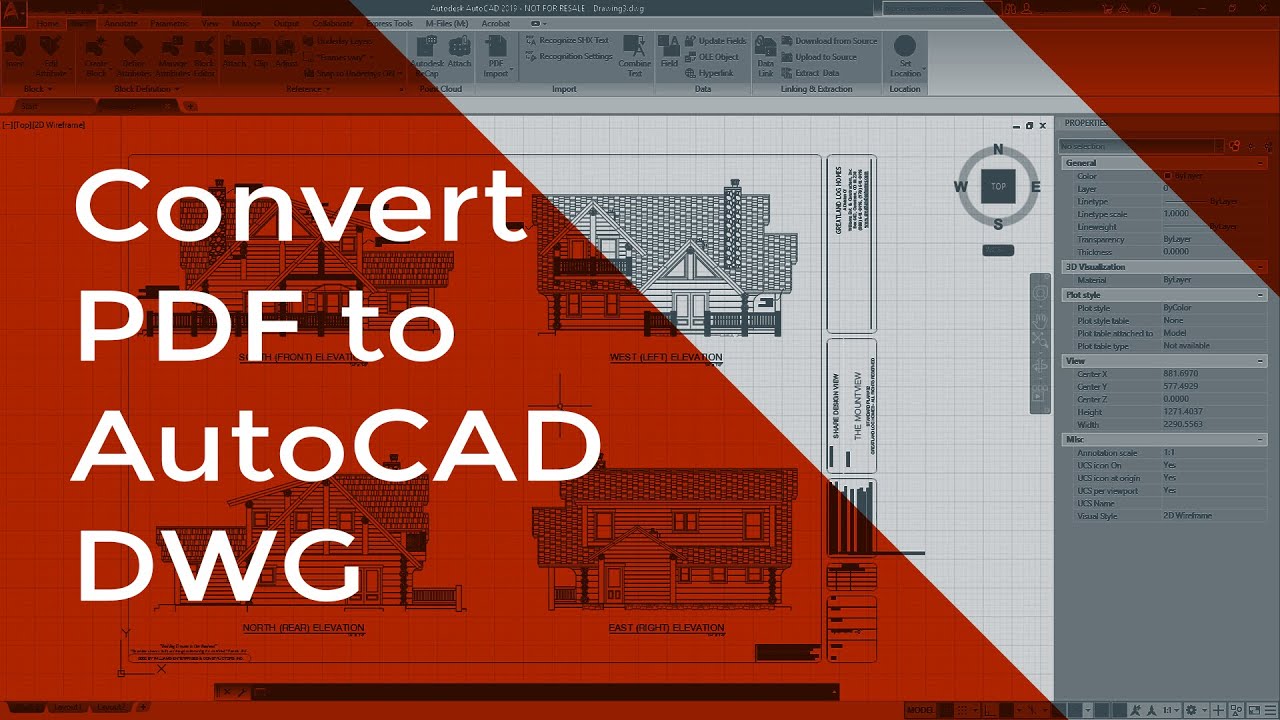
Okay, so you’ve got your PDF, and you need it in CAD format. No problem! There’s a whole bunch of software and online tools out there that can help you with that. Choosing the right one depends on your needs, budget, and the complexity of your PDFs. Let’s dive into some popular options.
Popular PDF to CAD Conversion Software and Online Tools
A quick rundown of some popular choices for converting PDFs to CAD files includes both standalone software and online services. Each has its own strengths and weaknesses, impacting the overall workflow and quality of the final CAD file. Consider factors like ease of use, the types of PDFs you’ll be working with (scanned, vector, etc.), and the specific CAD formats you need (AutoCAD DWG, DXF, etc.) when making your decision.
Software and Tool Feature Comparison
Let’s compare some key aspects: features, pricing models, and user interface. Ease of use varies widely, with some programs offering intuitive interfaces perfect for beginners, while others are more geared towards experienced CAD users. Pricing can range from free (often with limitations) to expensive professional-grade software. The features themselves determine the quality and accuracy of the conversion, impacting how well text, images, and lines translate from PDF to CAD.
Consider the types of PDFs you often work with; scanned documents often require more powerful OCR capabilities than clean, vector-based PDFs.
Specific Software Capabilities
Here’s a closer look at the individual strengths of some popular options. For instance, some software excels at handling complex scanned documents with advanced OCR (Optical Character Recognition), while others prioritize speed and simplicity for basic conversions. The ability to handle various CAD formats is also crucial; ensure the software supports the format you need (e.g., DWG, DXF, or others).
Some programs also offer advanced editing features within the CAD environment post-conversion.
Comparison Table of PDF to CAD Conversion Tools
Software | Pricing | User Interface | Key Features |
---|---|---|---|
Autodesk AutoCAD | Subscription-based | Advanced, powerful, but steep learning curve | Wide range of CAD formats, advanced editing tools, robust PDF import capabilities (often requires some manual cleanup). |
Adobe Acrobat Pro | Subscription-based | User-friendly, good for general PDF tasks, but CAD features are limited | Basic PDF to CAD conversion, often requiring additional cleanup and editing in a dedicated CAD program. |
Vector Magic | One-time purchase or subscription | Relatively user-friendly | Strong focus on image tracing and vectorization, good for converting scanned drawings. |
Online2CAD | Pay-per-conversion | Simple, web-based interface | Easy to use, suitable for quick conversions of simple PDFs. |
SolidWorks | Subscription-based | Powerful, but complex; high learning curve | Advanced 3D modeling capabilities; can import PDFs, but often requires significant manual work. |
Challenges and Limitations
Converting PDFs to CAD files isn’t always a walk in the park. The process can be surprisingly tricky, depending on the original PDF’s structure and complexity. Several factors can significantly impact the accuracy and usability of the resulting CAD file, leading to frustrating results if not properly addressed. Understanding these limitations is key to managing expectations and employing the right strategies for a successful conversion.
Image Quality Issues
The quality of the source PDF heavily influences the outcome. Scanned PDFs, in particular, often present challenges. Low-resolution scans result in blurry, pixelated CAD drawings, making precise measurements and editing extremely difficult. This is because the conversion software has to essentially “guess” at the lines and shapes from the pixels, leading to inaccuracies and jagged edges. Even high-resolution scans can sometimes struggle with subtle details or complex curves.
Vector-based PDFs, on the other hand, generally fare much better as they contain mathematical descriptions of the lines and shapes, providing a much cleaner conversion.
Text Recognition Problems
Extracting text from PDFs for inclusion in CAD drawings can be problematic. Optical Character Recognition (OCR) software, used to convert images of text into editable text, isn’t perfect. Handwritten text, stylized fonts, or poor image quality can all lead to inaccurate or missing text in the converted CAD file. This can be especially problematic if the text represents dimensions or annotations crucial to the design.
Advanced OCR software often helps, but perfect text extraction remains a challenge.
Complex Geometry Handling
Highly complex geometric shapes or intricate details within the PDF can be difficult for conversion software to handle accurately. The software might struggle to interpret the nuances of the design, resulting in simplified or distorted representations in the CAD file. This is particularly true for PDFs containing shaded or textured areas, which might not translate effectively into the line-based representations of most CAD software.
Impact of Different PDF File Structures
The conversion process is dramatically affected by the type of PDF. Scanned PDFs, essentially images of drawings, require OCR and image processing, leading to lower accuracy and more manual cleanup. Vector-based PDFs, containing mathematical representations of the drawings, usually convert more cleanly and accurately. Text-based PDFs, while potentially containing text data, often lack the graphical information necessary for direct CAD conversion, necessitating further steps.
This highlights the importance of understanding the source PDF’s structure before initiating the conversion.
Best Practices for Improving Conversion Quality
Improving the quality of converted CAD files requires a proactive approach. Here’s a list of best practices:
- Use High-Resolution Source PDFs: Higher resolution means more detail and better accuracy during conversion.
- Employ Advanced OCR Software: Opt for OCR software known for its accuracy and ability to handle complex fonts and layouts.
- Pre-process Scanned PDFs: Enhance scanned PDFs using image editing software to improve contrast and sharpness before conversion.
- Choose the Right Conversion Software: Select software specifically designed for PDF to CAD conversion and compatible with your CAD software.
- Manual Review and Editing: Always review and edit the converted CAD file to correct any inaccuracies or inconsistencies.
- Utilize Vector-Based PDFs Whenever Possible: Vector PDFs are inherently more suitable for CAD conversion, offering superior accuracy.
Accuracy and Fidelity of Conversion
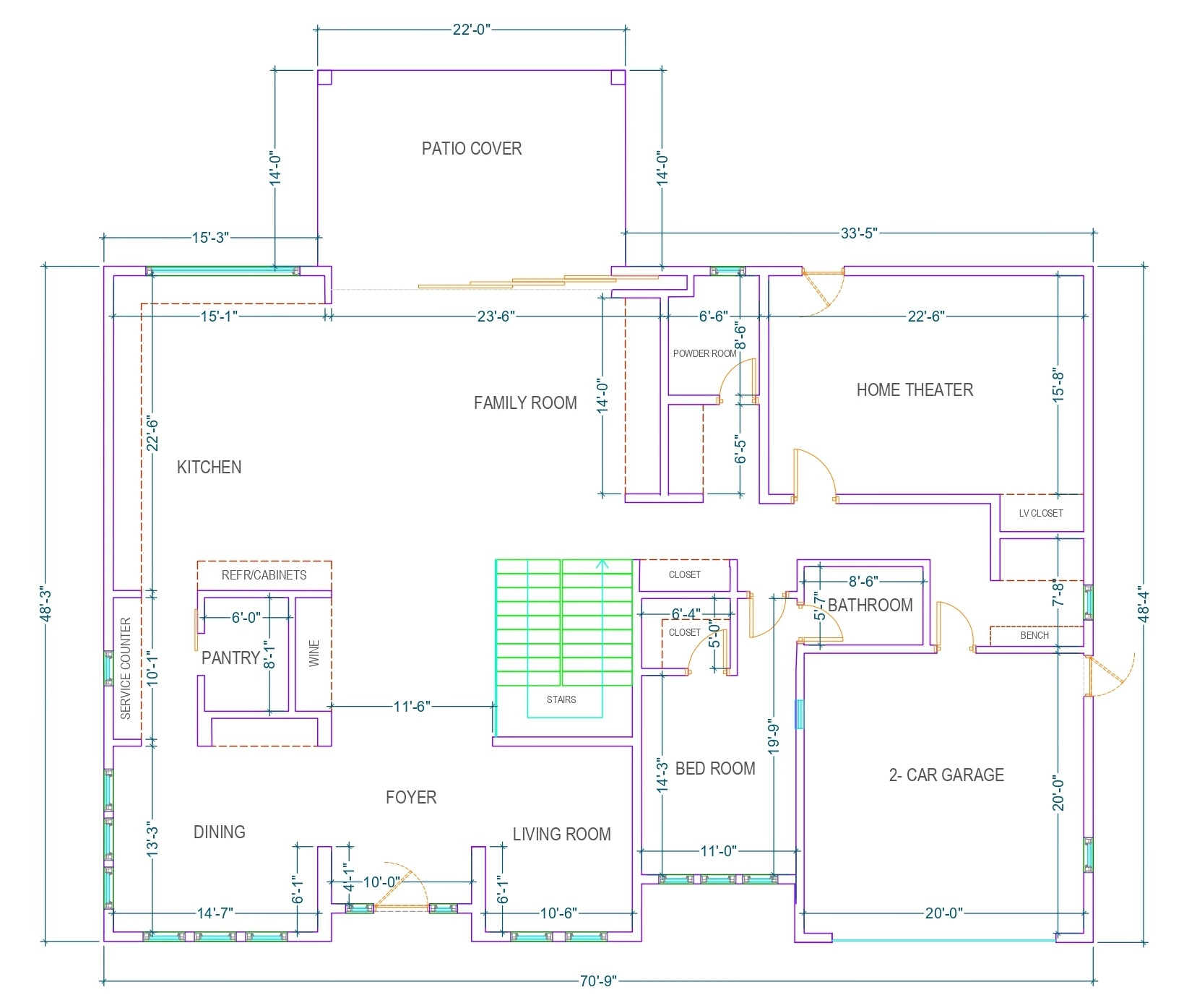
Converting PDFs to CAD files is rarely a perfect process. The accuracy and fidelity of the resulting CAD drawing depend heavily on several factors, making it crucial to understand these limitations before embarking on the conversion. A low-quality PDF will inevitably lead to a low-quality CAD file, regardless of the software used.
Factors Influencing Conversion Accuracy
Several key factors significantly impact the accuracy of PDF to CAD conversion. These include the original PDF’s quality (resolution, vector vs. raster graphics, compression), the chosen conversion method (optical character recognition or vectorization), and the capabilities of the conversion software itself. Higher-resolution PDFs generally produce more accurate results because they contain more detail. Vector-based PDFs, which use mathematical formulas to define shapes, usually convert more cleanly than raster-based PDFs (made of pixels), as they maintain their precision during the conversion.
However, even vector PDFs can suffer from inaccuracies if they contain complex or poorly defined geometry. The choice of conversion method also plays a critical role. Vectorization, which attempts to reconstruct vector graphics from the PDF, is generally preferred over OCR, which is better suited for text extraction.
Impact of PDF Characteristics on CAD Output Fidelity
The characteristics of the original PDF directly influence the fidelity of the resulting CAD file. For example, a low-resolution (72 dpi) PDF will likely produce a pixelated and inaccurate CAD drawing, especially when dealing with fine lines or intricate details. In contrast, a high-resolution (300 dpi or higher) PDF will generally yield a much more accurate conversion. Similarly, vector PDFs tend to preserve lines and curves more accurately than raster PDFs, which can lose detail during conversion, resulting in jagged lines or blurry images.
Consider a simple example: a circle drawn in a high-resolution vector PDF will maintain its smooth, perfect circular shape after conversion. The same circle in a low-resolution raster PDF might appear as a polygon with jagged edges after conversion.
Software Package Accuracy Comparison
Different software packages offer varying levels of accuracy in PDF to CAD conversion. Some specialized CAD conversion software may utilize advanced algorithms to improve accuracy, particularly when handling complex or problematic PDFs. While it’s difficult to provide a definitive ranking of software accuracy (as results can vary depending on the input PDF), it’s generally observed that dedicated conversion tools often outperform general-purpose PDF editors in terms of preserving geometric fidelity.
Users should carefully evaluate the software’s capabilities and features, and possibly test it with sample PDFs before committing to a purchase or subscription.
Impact of Various Factors on Conversion Accuracy
The table below illustrates the general impact of several factors on conversion accuracy. Note that these are generalizations, and actual results can vary depending on the specific PDF, software used, and conversion settings.
Factor | Low Impact | Medium Impact | High Impact |
---|---|---|---|
PDF Resolution | 300 dpi+ | 150-300 dpi | <72 dpi |
PDF Type (Vector/Raster) | Vector | Mixed Vector/Raster | Raster |
Drawing Complexity | Simple Drawings | Moderate Complexity | Highly Complex Drawings with many small details |
Software Quality | Specialized CAD Conversion Software | General-Purpose PDF Editors with Conversion Features | Free or Low-Cost Conversion Tools |
Pre-processing Techniques for PDFs
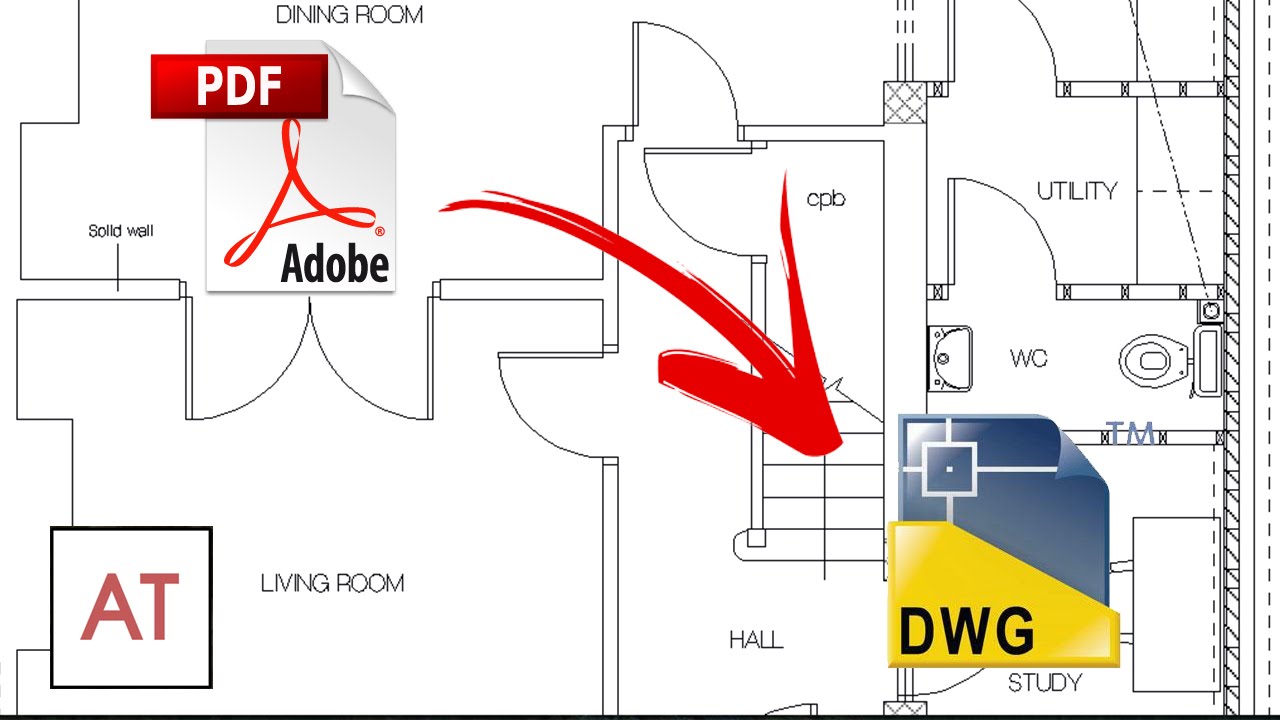
Getting a clean, accurate CAD file from a PDF often hinges on the pre-processing steps you take. Think of it like prepping ingredients before cooking – the better the prep, the better the final dish. Proper pre-processing significantly improves the conversion process, reducing errors and increasing the fidelity of the resulting CAD model. This involves cleaning up the PDF, enhancing its visual quality, and preparing it for the conversion software to do its job efficiently.
Image Enhancement Techniques for Scanned PDFs
Scanned PDFs, especially those from older documents, often suffer from issues like low resolution, uneven lighting, and noise. These imperfections can severely impact the accuracy of a CAD conversion. Image enhancement techniques address these problems. For example, sharpening tools can improve the definition of lines and curves, making them easier for the conversion software to interpret. Noise reduction filters can smooth out grainy areas caused by the scanning process, minimizing spurious data.
Techniques like contrast adjustment and brightness correction can improve the overall clarity and readability of the image, ensuring lines are clearly defined and text is easily legible. Consider histogram equalization to distribute pixel intensities more evenly, enhancing the overall contrast and visibility of details.
The Role of Optical Character Recognition (OCR)
Optical Character Recognition (OCR) is crucial for converting text within PDFs to editable CAD text. Many CAD programs use text as a crucial element in defining geometry and dimensions. OCR software analyzes the image of the text, identifying individual characters and converting them into a machine-readable format. This allows you to edit text directly within your CAD software, rather than manually redrawing text elements, which is a significant time saver and reduces potential errors.
The accuracy of OCR depends on the quality of the scanned PDF; hence, image enhancement techniques mentioned previously are critical for successful OCR. Choosing the right OCR engine tailored to the specific font and language used in the PDF can further improve the accuracy of the text conversion.
Step-by-Step Guide for Pre-processing a Scanned PDF
Before converting a scanned PDF to CAD, follow these steps for optimal results:
- Scan at High Resolution: Begin with a high-resolution scan (at least 300 DPI). Higher resolution captures more detail, leading to a more accurate conversion. Lower resolutions result in blurry lines and loss of detail, creating significant challenges during the conversion.
- Image Enhancement: Use image editing software to improve the quality of the scan. This includes adjusting brightness and contrast, sharpening blurry lines, and reducing noise. Experiment with different filters to find the best balance between detail and clarity. Remember, over-sharpening can create artifacts, so a subtle approach is often best.
- Deskew the Image: If the scanned document is skewed, straighten it using image editing software. This ensures that lines and shapes are accurately represented in the CAD model, preventing distortions and inaccuracies.
- Apply OCR: Use OCR software to convert any text in the PDF to editable text. This is crucial for preserving textual information, such as dimensions and annotations, within the CAD model.
- Clean Up Artifacts: Manually remove any remaining artifacts or imperfections that the image enhancement and OCR processes didn’t address. This might include stray marks, smudges, or incomplete lines. This final step ensures the cleanest possible input for the PDF to CAD conversion software.
Following these steps helps ensure a smoother, more accurate conversion, resulting in a high-fidelity CAD model.
Post-processing and Editing of CAD Files
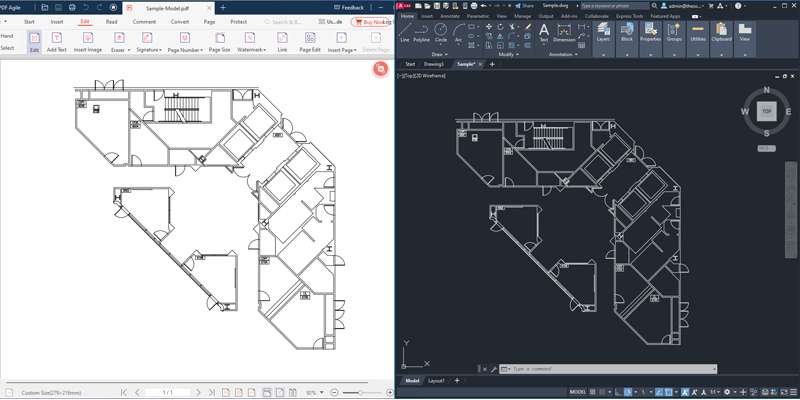
Okay, so you’ve wrestled your PDF into a CAD file. Congrats! But the conversion process isn’t always perfect. Think of it like a really rough draft – it needs some serious editing before it’s ready for prime time. This post-processing stage is crucial for ensuring accuracy and usability of your newly minted CAD drawing. We’ll cover the essential steps and tools you’ll need to get that CAD file looking ship-shape.Post-processing involves cleaning up the geometry resulting from the PDF to CAD conversion.
This often means dealing with inconsistencies, errors, and generally messy lines and shapes. The goal is to create a clean, accurate, and complete CAD model that’s ready for further design work or manufacturing processes. The level of effort required will depend heavily on the quality of the original PDF and the conversion method used. A poorly scanned PDF will obviously require more post-processing than a clean, vector-based PDF.
Geometry Cleanup and Error Correction
This is where the real work begins. Common issues include overlapping lines, gaps in lines, extraneous geometry (like stray lines or points), and inaccurate dimensions. You’ll need to carefully inspect the converted CAD file, identifying and fixing these problems. Tools like the “trim,” “extend,” “fillet,” and “chamfer” commands in most CAD software are your best friends here.
For example, you might use the trim command to remove overlapping line segments, or the extend command to close gaps in lines representing a wall or boundary. Think of it like a digital cleanup crew, meticulously tidying up the CAD drawing.
Editing and Modifying Converted CAD Files
Once the initial cleanup is done, you may need to make further modifications to ensure the CAD file accurately reflects the original PDF’s intent. This could involve adding missing geometry, adjusting dimensions, or modifying existing elements. This step might require referring back to the original PDF to confirm details or make informed decisions. For instance, if a dimension is slightly off, you’ll want to cross-reference it with the PDF to confirm the correct value.
This back-and-forth process ensures fidelity between the source PDF and the final CAD model.
Using CAD Software Tools for Geometry Refinement
Most CAD software packages are loaded with tools designed for precisely this type of work. Beyond the basic editing commands mentioned earlier, you might employ more advanced features like:
- Boolean operations: These let you combine, subtract, or intersect different geometric elements to create complex shapes. For example, subtracting a circular cutout from a rectangular shape to model a hole.
- Constraint-based modeling: This allows you to define relationships between geometric elements (like parallelism or perpendicularity), ensuring that modifications to one element automatically update related elements, maintaining consistency and accuracy.
- Layer management: Organizing elements into layers helps manage complexity, making it easier to select, edit, and manipulate specific parts of the drawing.
Effective use of these tools significantly accelerates the post-processing workflow and ensures a high-quality final product.
Post-Processing Checklist
Before declaring victory, run through this checklist to make sure you’ve covered all the bases:
- Visual Inspection: Thoroughly review the entire drawing for any obvious errors or inconsistencies.
- Geometry Cleanup: Remove overlapping lines, gaps, and extraneous geometry.
- Dimension Verification: Check all dimensions against the original PDF and make any necessary corrections.
- Layer Organization: Organize elements into logical layers for better management.
- Attribute Verification: Ensure all elements have the correct attributes (e.g., layer, color, line type).
- Final Review: Perform a final review to ensure accuracy and completeness.
Following this checklist helps ensure a high-quality, accurate, and complete CAD model from your PDF conversion efforts. Remember, patience and attention to detail are key to successful post-processing.
File Formats and Compatibility
Picking the right CAD file format after converting your PDF is crucial. The format you choose directly impacts how easily other software can open and use your newly created CAD drawing, and even influences the level of detail preserved. Different formats have different strengths and weaknesses, so understanding these differences is key to a successful conversion.Choosing a CAD file format isn’t just about opening the file; it affects how well the software can edit, modify, and utilize the data within.
For example, some formats are better suited for 2D drafting, while others excel at handling 3D models and complex assemblies. This section will clarify these differences to help you make an informed decision.
Common CAD File Formats and Software Compatibility
Several common CAD file formats exist, each with varying degrees of compatibility across different software packages. AutoCAD’s native format, DWG, is widely supported, but DXF offers broader interoperability. Other formats, such as STEP and IGES, are commonly used for exchanging data between different CAD systems, particularly in collaborative projects or when dealing with multiple software packages. The choice of format impacts the ability to share and collaborate on the design.
For instance, a DWG file might open seamlessly in AutoCAD but require a plugin or conversion in a different CAD program.
Implications of Choosing Different CAD File Formats
The choice of output format significantly influences the final CAD file’s size, data integrity, and overall usability. DWG files, while generally highly detailed, can be larger than other formats. DXF, designed for exchange, often sacrifices some detail for compatibility. Choosing a compressed format might reduce file size but might also lead to a loss of information, affecting the accuracy of the final product.
Consider the trade-offs between file size, detail preservation, and software compatibility when selecting your output format. For example, if you need to send the file to a collaborator using a different CAD program, DXF is generally a safer bet for compatibility, even if it results in a slightly larger file size than a DWG.
Choosing the Most Suitable CAD Format for a Given Application
Selecting the optimal CAD format depends heavily on the intended application and the software involved. For projects primarily using AutoCAD, DWG is usually the best choice, maximizing detail and functionality. However, for sharing with various CAD systems or for archiving purposes, DXF’s broader compatibility makes it more suitable. If the project involves 3D modeling and requires high fidelity across different software packages, formats like STEP or IGES might be preferred.
For instance, a large architectural project intended for multiple collaborators across different firms might benefit from using DXF or STEP for broader compatibility and data exchange.
CAD File Format Characteristics and Compatibility
Format | Description | Software Compatibility | Strengths |
---|---|---|---|
DWG | Autodesk’s native format; highly detailed | Primarily AutoCAD and AutoCAD-related software; often requires plugins in other software. | High detail, native AutoCAD support |
DXF | Drawing Exchange Format; widely compatible | Most CAD software; good interoperability | Broad compatibility, good for data exchange |
STEP | Standard for the Exchange of Product model data; 3D model format | Wide range of CAD and CAM software | Excellent for 3D model exchange, neutral format |
IGES | Initial Graphics Exchange Specification; another neutral format for 3D models | Wide range of CAD and CAM software | Good for 3D model exchange, neutral format |
Applications and Use Cases: Pdf To Cad
PDF to CAD conversion isn’t just some geeky tech trick; it’s a vital tool impacting numerous industries. Its ability to bridge the gap between digital documents and design software makes it incredibly useful for streamlining workflows and improving efficiency. This process saves time and resources, allowing professionals to focus on the creative and analytical aspects of their projects rather than tedious manual redrawing.PDF to CAD conversion finds its application in diverse scenarios, offering significant advantages across various professional contexts.
The ability to reuse existing PDF drawings, regardless of their origin, significantly reduces the need for recreating them from scratch. This is especially beneficial when dealing with legacy documents or collaborating with parties who only provide PDFs. The resulting CAD files can then be seamlessly integrated into existing projects, enhancing collaboration and accelerating project timelines.
Architectural Design
Architects frequently receive design plans, specifications, and even hand-drawn sketches as PDFs. Converting these to CAD allows for easy integration into Building Information Modeling (BIM) software. This facilitates precise measurements, modifications, and collaboration with structural engineers and contractors. For instance, an architect might receive a site survey as a PDF from a surveyor. Converting this to CAD allows them to accurately overlay the survey data onto their building design in their CAD software.
This ensures that the building design is compatible with the site conditions.
Engineering
In engineering, PDFs are often used for blueprints, schematics, and technical drawings. Conversion to CAD enables engineers to modify existing designs, perform simulations, and generate detailed manufacturing instructions. Imagine a mechanical engineer receiving a PDF of a component’s design from a subcontractor. Converting this to CAD lets the engineer seamlessly integrate the component into their larger assembly, making modifications, and generating detailed manufacturing drawings.
Manufacturing
Manufacturers often receive product designs and specifications as PDFs. Converting these to CAD allows for precise manufacturing processes, CNC machining, and automated production line programming. For example, a manufacturer might receive a design for a custom part as a PDF. Converting this PDF to CAD allows the manufacturer to program their CNC machines to precisely manufacture the part.
This eliminates manual programming, improving accuracy and reducing production time.
Construction
Construction projects often involve a variety of documents, including shop drawings, specifications, and as-built drawings. Converting these PDFs to CAD helps in coordinating different aspects of the project, ensuring accuracy, and avoiding conflicts. A contractor might receive a PDF of the structural steel design for a building. Converting it to CAD allows the contractor to coordinate the steel erection with other construction activities, preventing potential clashes and delays.
Industries Benefiting from PDF to CAD Conversion
The advantages of PDF to CAD conversion are widespread. Here are some industries that significantly benefit:
- Architectural Design: Integrating PDF plans into BIM software for precise modeling and collaboration.
- Engineering (Mechanical, Electrical, Civil): Modifying designs, performing simulations, and creating manufacturing instructions.
- Manufacturing: Precisely programming CNC machines and automating production lines.
- Construction: Coordinating different project aspects and avoiding conflicts.
- GIS and Mapping: Integrating scanned maps and surveys into GIS software for analysis and updating.
- Real Estate: Digitizing property plans and creating accurate property records.
Cost Considerations and ROI
Converting PDFs to CAD files isn’t free; it involves a mix of upfront costs and ongoing expenses. Understanding these costs and how they relate to the benefits you gain is crucial for making smart decisions. This section breaks down the financial aspects of PDF to CAD conversion and provides strategies for maximizing your return on investment.Software licenses, labor costs, and the time spent on conversion are all significant factors.
The choice of conversion method—manual tracing, automated software, or a hybrid approach—directly impacts these costs. A thorough cost-benefit analysis is essential before committing to a specific method.
Software Licensing Costs
The cost of software significantly impacts the overall expense. High-end CAD software packages can cost thousands of dollars per license, while simpler PDF to CAD converters might be available for a few hundred dollars or even as a subscription service. Free, open-source options exist, but they often require more technical expertise and may have limitations in functionality and accuracy.
Consider the features you need and whether the cost of a premium license justifies the increased speed, accuracy, and support. For example, a large architectural firm might justify the expense of high-end software due to the volume of conversions and the need for precise results, whereas a small business might find a more affordable option sufficient.
Labor Costs and Time Investment
Manual tracing is labor-intensive and time-consuming, leading to high labor costs. The time spent on pre-processing, conversion, and post-processing needs to be considered. Automated software significantly reduces manual effort, thus lowering labor costs and speeding up the entire process. However, even with automated tools, some level of manual intervention and editing is usually necessary, which still incurs labor costs.
The hourly rate of the personnel involved directly influences the overall cost. A skilled CAD technician will naturally command a higher hourly rate than a less experienced individual, reflecting in the total project cost.
Return on Investment (ROI) Assessment
Assessing ROI involves comparing the total cost of conversion with the benefits gained. Benefits can include increased efficiency, reduced errors, improved project timelines, and the ability to reuse data in other projects. For instance, converting a set of PDF architectural drawings to CAD format might save significant time during the design and construction phases, leading to cost savings and potentially earlier project completion.
The ROI can be calculated using a simple formula:
ROI = (Net Profit / Total Investment) – 100%
Where Net Profit is the difference between the benefits gained (e.g., time saved, reduced errors, increased efficiency) and the total cost of conversion. The challenge lies in quantifying the intangible benefits like improved design efficiency.
Strategies for Minimizing Costs, Pdf to cad
Several strategies can help minimize the costs associated with PDF to CAD conversion. Using automated software can significantly reduce labor costs and time. Investing in proper training for staff can improve efficiency and reduce errors, lowering the need for extensive post-processing. Outsourcing the conversion to specialized services might be cost-effective for businesses lacking in-house expertise. Careful pre-processing of PDFs, ensuring high-quality scans and clean files, can improve conversion accuracy and reduce post-processing time.
Converting PDFs to CAD files can be a real pain, especially when dealing with complex drawings. Finding the right software is key, and that often depends on your operating system; if you’re using microsoft windows , you’ll have a ton of options to choose from. Ultimately, the best approach for PDF to CAD conversion depends on your specific needs and the complexity of your PDF files.
Hypothetical Cost-Benefit Analysis
Let’s consider a hypothetical scenario: An architectural firm needs to convert 50 PDF drawings.* Method 1: Manual Tracing: Cost: $5000 (labor costs) + $0 (software). Time: 250 hours.
Method 2
Automated Software: Cost: $2000 (software license) + $1000 (labor costs). Time: 50 hours.Assuming each hour saved translates to $50 in increased efficiency, Method 2 yields a net savings of $10,000 (200 hours saved x $50/hour) – $3000 (software + labor) = $7000. This represents a significant ROI compared to manual tracing.
Last Point
So, there you have it – a comprehensive look at the wild world of PDF to CAD conversion. While the process can be tricky, understanding the different methods, software options, and potential pitfalls empowers you to make informed decisions. Remember to choose the method that best suits your needs, considering factors like accuracy, time constraints, and budget. With a little planning and the right tools, you can successfully navigate this conversion process and achieve the precise CAD drawings you need.
Now go forth and conquer those PDFs!
Detailed FAQs
What are the most common CAD file formats?
The most common are DWG (AutoCAD’s native format), DXF (a more universal format), and DGN (MicroStation’s format). The best choice depends on your CAD software and project requirements.
Can I convert a scanned PDF to CAD?
Yes, but it’s usually more challenging and requires OCR (Optical Character Recognition) software to convert text and potentially manual tracing or vectorization to recreate lines and shapes. Expect lower accuracy compared to vector-based PDFs.
How much does PDF to CAD conversion software cost?
Costs vary wildly, from free online tools with limited functionality to professional-grade software costing hundreds or even thousands of dollars. Consider your needs and budget when selecting software.
What if my converted CAD file is inaccurate?
Thorough pre- and post-processing are crucial. Post-processing in your CAD software will almost always be necessary to clean up and refine the converted geometry.
Are there any free PDF to CAD converters?
Yes, several free online converters exist, but they usually have limitations on file size, functionality, and accuracy. They might be great for small, simple files but not for large, complex projects.